SIMULATEUR DE TELESCOPIQUE MANITOU
INTRODUCTION
Chez Arkaï Interactive, nous avons récemment collaboré avec le groupe Manitou pour concevoir un simulateur de télescopique innovant, alliant une cabine physique réaliste à une simulation virtuelle développée sur Unreal Engine 5.
Ce projet vise à tester de nouvelles interfaces utilisateur (UI/UX) et des éléments physiques en conditions quasi réelles.
Le simulateur se compose d’une cabine équipée d’un habitacle, d’un fauteuil, d’un volant et de joysticks, associés à une simulation virtuelle immersive.
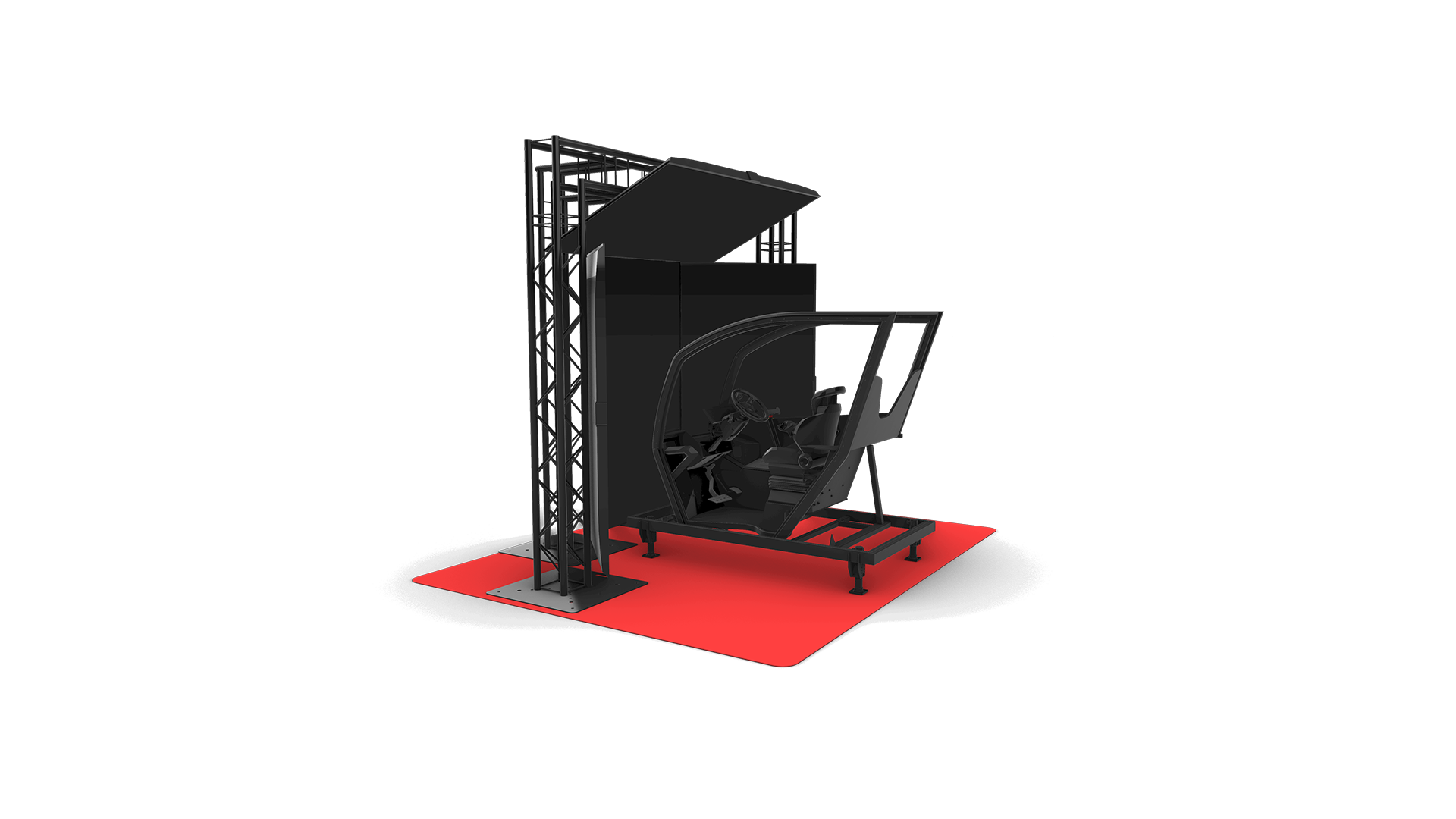
L’objectif est de permettre aux équipes de R&D de Manitou d’évaluer efficacement de nouvelles conceptions en offrant une expérience utilisateur réaliste.
Pour cela, ils ont choisis de créer un prototype mixte , à la fois physique et numérique. Mais pourquoi un simulateur au lieu d’un Prototype Physique seul ? Il y a 3 raisons principales à ce choix :
- Agilité : Les modifications peuvent être rapidement implémentées et testées.
- Itérations rapides et nombreuses : Les cycles de développement sont accélérés, permettant une optimisation continue.
- Coûts réduits : La nécessité de construire plusieurs prototypes physiques est éliminée, réduisant ainsi les dépenses.
Mais créer un simulateur qui reproduise des conditions quasi réelles n’est pas si simple. Pour garantir une
immersion réussie, la liaison des éléments physiques et virtuels doit être parfaite. Plusieurs éléments clés sont
à garder en tête tout au long du développement :
- Comportement réaliste du véhicule : La direction, les systèmes de sécurité, les suspensions et autres fonctionnalités doivent refléter fidèlement le fonctionnement réel du télescopique.
- Rendu visuel immersif : L’utilisation d’ombres, de lumières et d’environnements détaillés assure un visuel convaincant.
- Immersion totale : Des écrans panoramiques et un design sonore élaboré renforcent le sentiment d’immersion.
- Technologie haptique * : L’intégration de vérins autour de la cabine offre des sensations retours physiques réalistes.
- Éléments manipulables réels : L’utilisation de composants physiques tels que le cockpit, le volant et les pédales améliore l’authenticité de l’expérience.
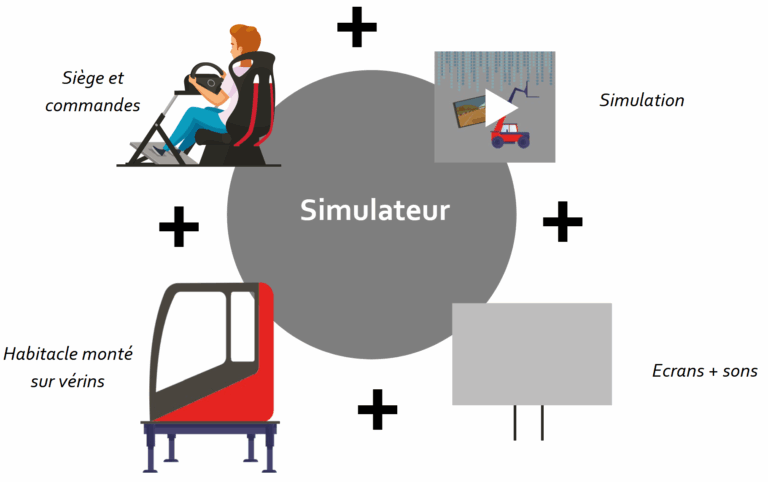
LES ACTEURS DU PROJET
Plusieurs partenaires ont contribué au succès de ce projet :
- Services R&D Manitou Groupe : Prototypage, design, ergonomie, UI/UX, électronique.
- D-Box : Fourniture du système haptique (vérins).
- Arkaï Interactive : Développement de l’environnement 3D et de la simulation
Pourquoi Arkaï Interactive a été sélectionné pour réaliser ce projet ?
Avant de fonder Arkaï Interactive, notre équipe possédait une solide expérience dans le secteur industriel. Cédric, en tant que chef de projet et dessinateur industriel, et Julian, en tant que dessinateur industriel et développeur, maîtrisaient les méthodes de travail du secteur et comprenaient les enjeux d’un tel projet pour Manitou.
De plus, au sein d’Arkaï Interactive nous avions déjà réalisé un projet similaire, notre simulateur de chariot élévateur, qui, bien que plus simple, nous a permis d’avoir une véritable expertise. Ce projet sur-mesure nous a permis d’aller encore plus loin, à la frontière entre notre offre de prototypage numérique de produit et notre simulateur destiné à la formation.
Enfin, c’est notre connaissance pointue du moteur Unreal Engine 5 qui nous a permis de participer à ce projet et notamment du moteur physique Chaos. Parmi les possibilités apportée par ce moteur, on peut notamment citer la gestion de systèmes mécaniques complexes avec des vérins, moteurs, pivots fonctionnant ensembles ou encore la prise en charge du mode de physique asynchrone, permettant de réaliser les calculs physiques en parallèle sans ralentir le visuel de la simulation.
Nous remercions les équipes Recherche et Développement de Manitou France pour la confiance accordée et pour cette collaboration fructueuse.
L'Ecriture du scenario
La définition du scénario est une étape cruciale pour tester de nouvelles UI/UX ou des éléments physiques en situation réelle.
Pour chaque élément à tester (nouvelle ergonomie, nouveau design, nouvelle fonctionnalité), l’équipe R&D de Manitou a élaboré plusieurs scènes avant de sélectionner celle qui permettrait de tester au mieux la nouveauté. Nous avons ensuite identifié les éléments à ajouter pour le bon déroulement du scénario, que ce soit en terme de modélisation (objets, décors), d’animation (objets lourds) ou même d’ambiance sonore (bruits de chute).
L'ENVIRONNEMENT
Pour créer l’environnement de test, Manitou a réalisé un Sourcing photo, vidéo et sonore afin de répertorier les éléments indispensables de l’expérience. Ils ont finalement opté pour une zone de construction de bâtiment constituée d’un bâtiment en construction, de zones avec des matériaux de construction déplaçables, de zones complexes avec du relief sur le sol, de couloir de passage destinés aux engins…
En nous appuyant sur les scènes du scénario, nous avons créé des éléments à manutentionner, implémenté de nouveaux sons pour enrichir le scénario et travaillé sur l’éclairage (Lighting) pour permettre un mode jour/nuit.
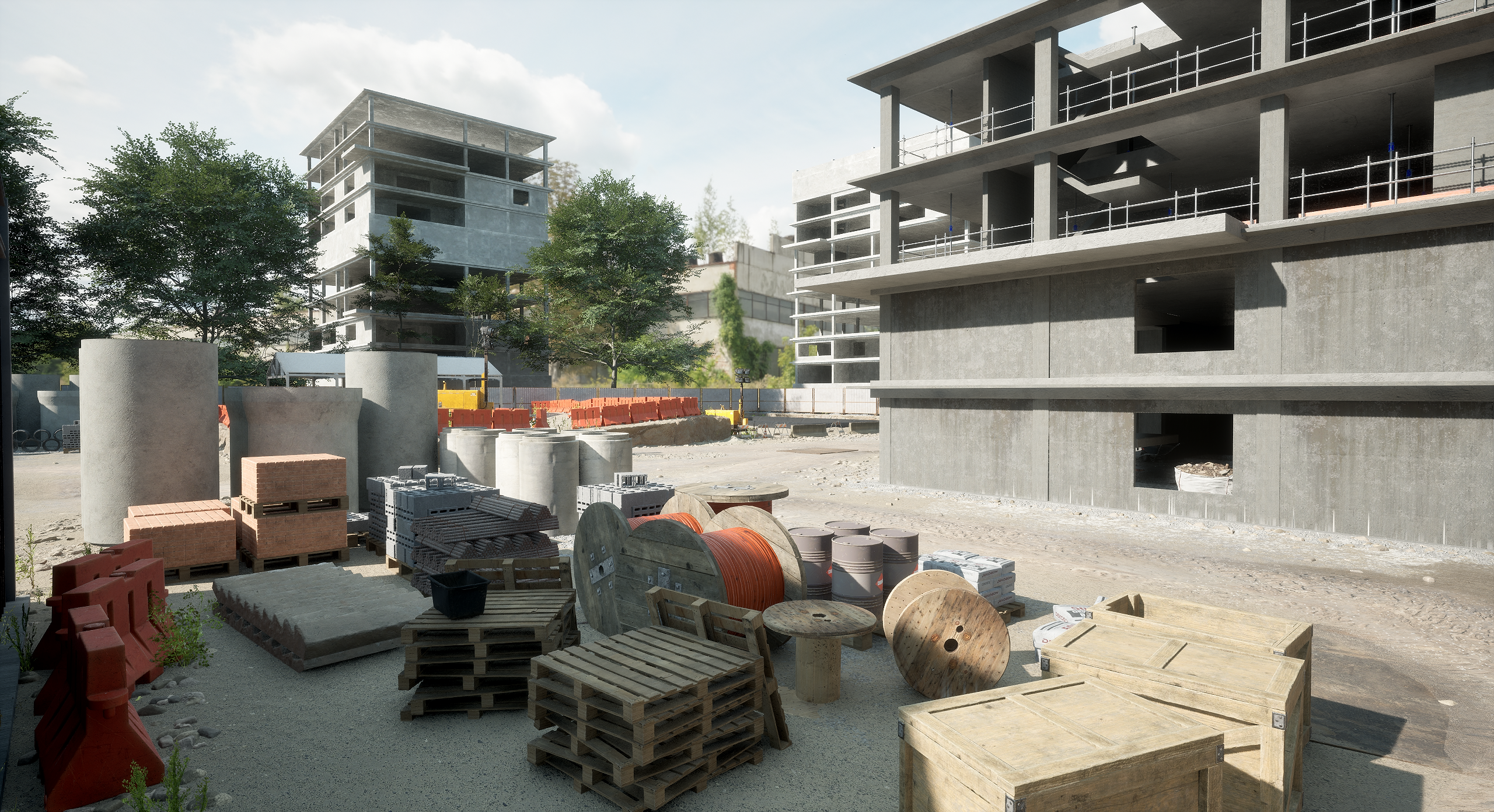
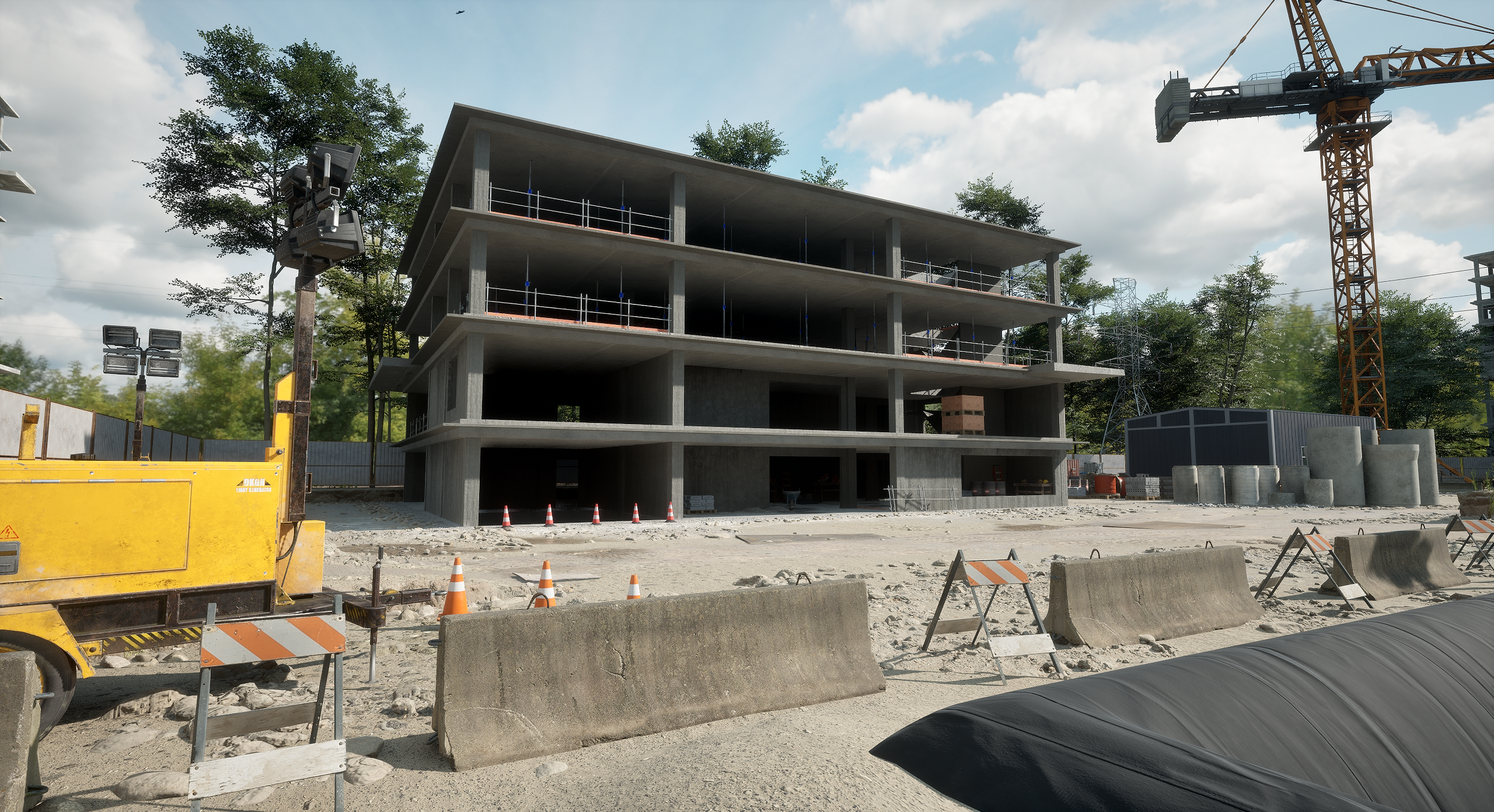
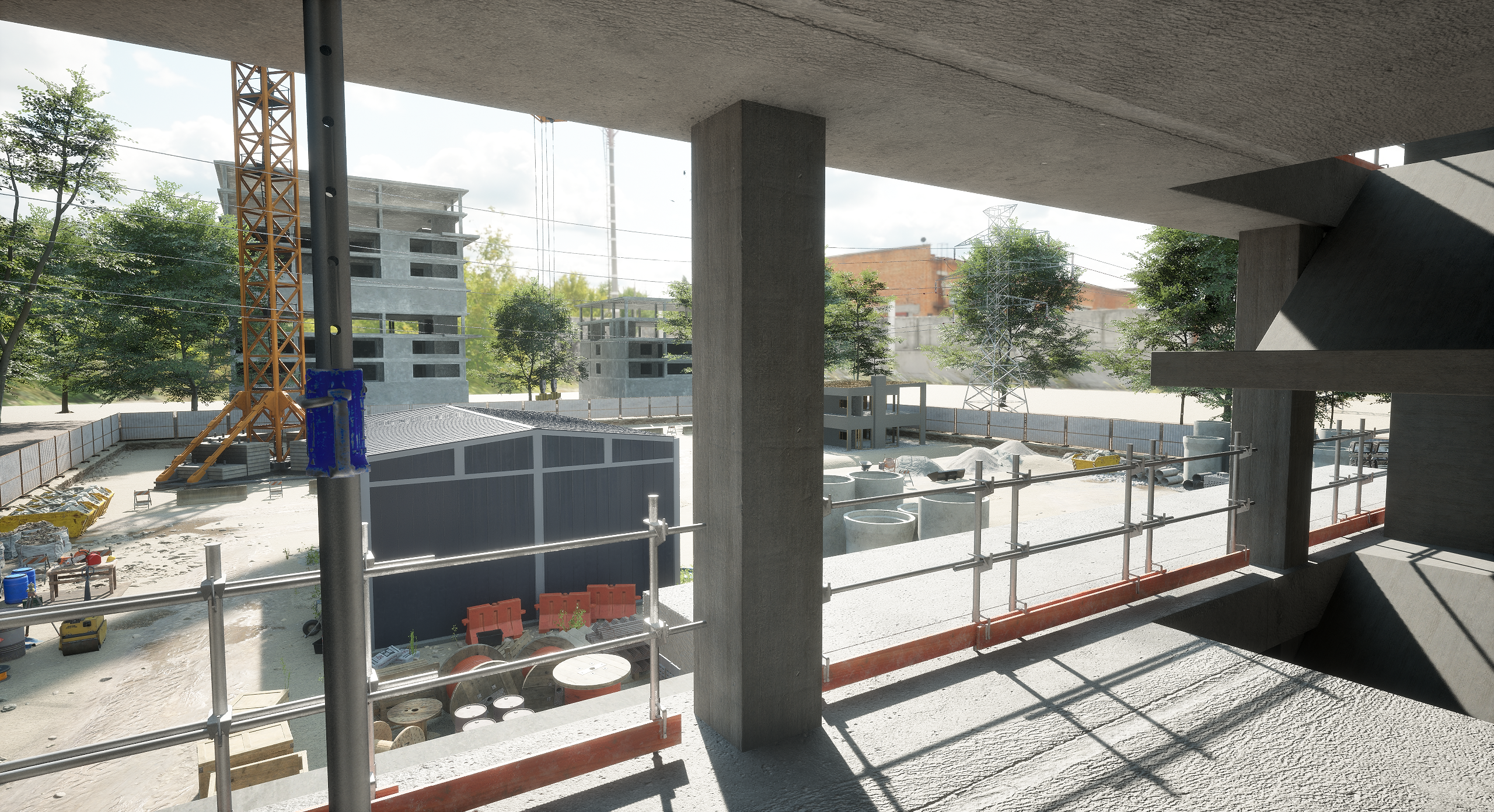
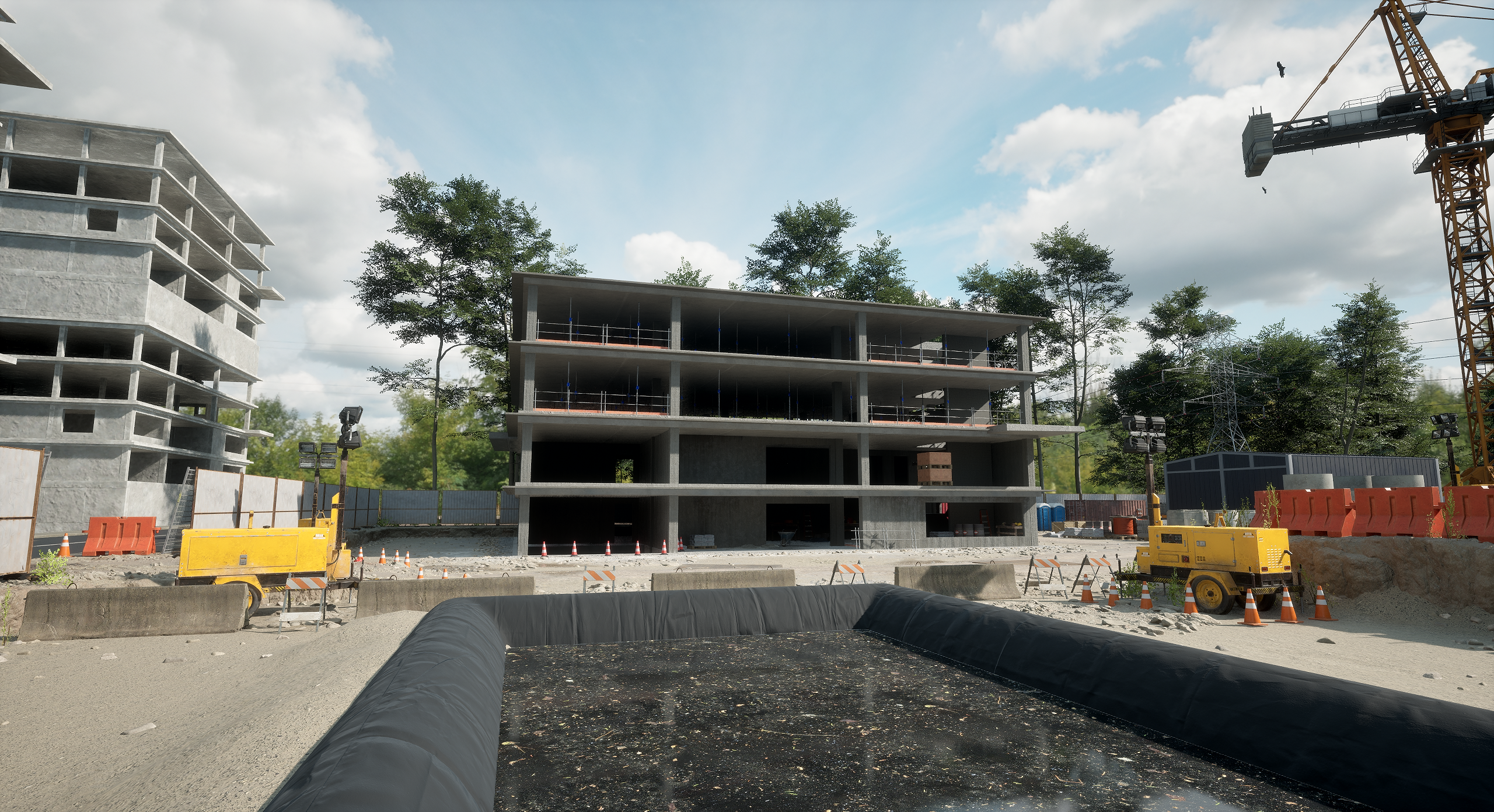
LA CREATION DU VEHICULE
LE PROTOTYPE PHYSIQUE DU TELESCOPIQUE : UNE CABINE REALISTE POUR UNE EXPERIENCE IMMERSIVE
La cabine du simulateur, ainsi que tous ses éléments physiques (volant, fauteuil, commandes…), ont été conçus avec précision par les équipes de Manitou. Ces éléments sont directement manipulables par l’utilisateur, garantissant des tests en conditions optimales. Grâce à des technologies avancées comme l’impression 3D, l’usinage CNC, le moulage et la découpe laser, chaque composant a été fabriqué avec le plus grand soin pour offrir une expérience utilisateur au plus proche de la réalité. C’est également à cette étape que les écrans, les enceintes, les interfaces homme-machine (IHM) et le système haptique sont intégrés. Ces dispositifs jouent un rôle clé dans l’interaction avec le véhicule, servant à la fois de commandes (via les IHM) et de retour d’information (bruit, vibrations, images…).
Le système haptique, développé par D-Box, spécialiste canadien des technologies haptiques, apporte une dimension supplémentaire à l’expérience en simulant avec précision les mouvements et sensations d’un télescopique en action. Une technologie de pointe utilisée dans l’industrie du cinéma, les simulateurs de course et la formation professionnelle.
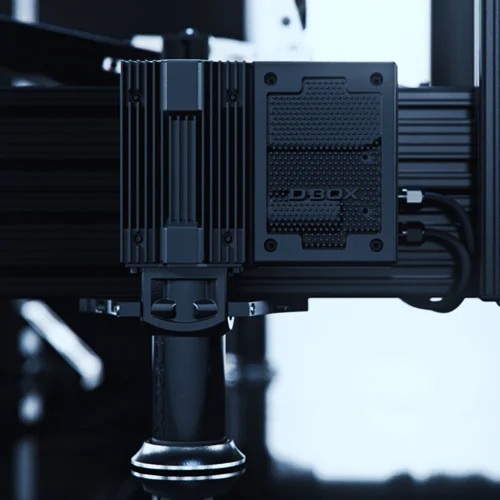
LA MODELISATION 3D Du vehicule : un jumeau numérique prend vie
À partir de la modélisation 3D réalisée par les équipes de Manitou, nous avons préparé le véhicule pour l’intégrer à notre moteur Unreal Engine. Cette étape est cruciale pour le bon fonctionnement de l’ensemble du projet. Nous avons séparé certaines pièces, simplifié d’autres pour gagner en légèreté, remodélisé certains éléments problématiques et ajouté divers accessoires.
Reste ensuite l’étape de l’habillage du modèle 3D : le texturing. Cette étape permet d’apporter du réalisme à la scène en ajoutant des couleurs et des textures. Pour cela, Arkaï Interactive s’appuie sur des images réelles et des photos de matériaux. Les détails sont important (rayure, ombres, tâches…) car une scène trop lisse perd toute crédibilité.
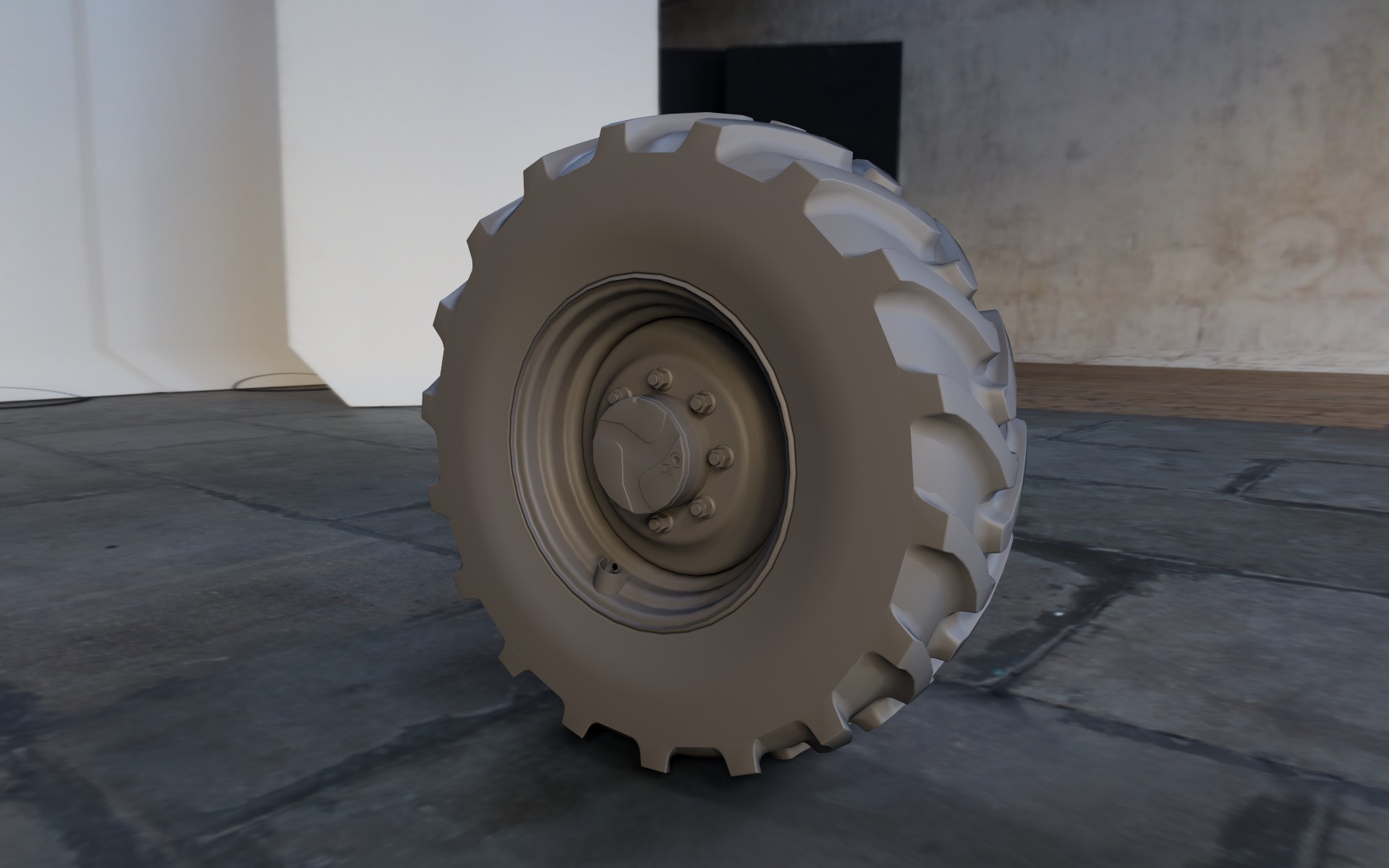

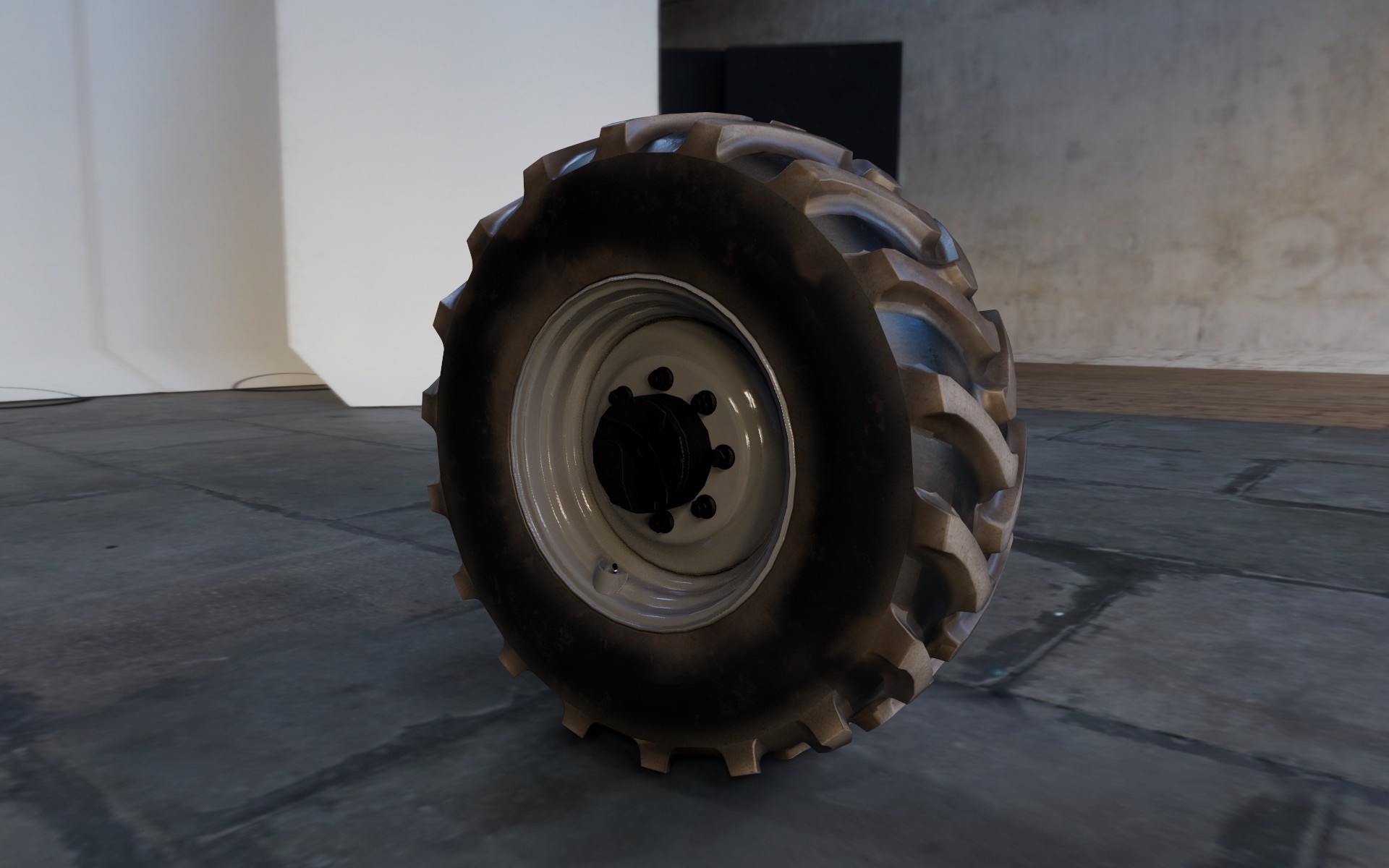
CODER LE DEPLACEMENT ET LA PHYSIQUE POUR DONNER VIE AU VEHICULE
Une fois le télescopique modélisé en 3D, arrive la grosse étape de développement : le codage de la physique. On parle ici de reproduire à l’identique le comportement d’un télescopique (très éloigné du comportement de tout autre véhicule). S’agissant ici de créer une simulation au plus proche du réel, impossible de ne pas s’adapter au comportement particulier du télescopique sous peine de « casser » l’immersion. Le codage de la physique a donc dû être réalisé sur-mesure.
Grâce à la fiche technique du télescopique, nous avons pu récupérer les informations de dimensions comme l’angle de déversement, le rayon de braquage mais également de performances comme la vitesse de déplacement, le temps de levage… A l’aide de ces données techniques et de nombreux calculs, nous avons codé les différents Modes et options :
- Direction (crabe/4RD/2RD), les modes lent, rapide, sécurité, blocage différentiel, mode marche AR (avec le déclenchement de la caméra de recul),
- Manutention : levage, infos, pesé de la charge porté, détacher l’accessoire
- Conduite : stabilisateurs, suspensions, vitesse résiduelle, freinage
LIAISON DU PROTOTYPE PHYSIQUE ET VIRTUEL : A LA RECHERCHE DE LA SYNCHRONISATION PARFAITE
Une fois le comportement physique du simulateur codé, il a fallu s’atteler à la liaison avec les éléments réels du prototype physique. Concrètement, il s’agit de récupérer et intégrer les données des périphériques d’entrée et de sortie (écrans, volant, joysticks, pédales, Interfaces Homme-Machine ou IHM, vérins…).
C’est l’un des défis majeurs du projet : assurer une liaison parfaite entre le prototype physique et la simulation virtuelle pour garantir une immersion totale. Le volant et les pédales déclenchent-ils bien les actions attendues ? Les écrans affichent-ils la bonne perspective en temps réel ? Le son est-il correctement spatialisé pour une immersion optimale ? Les vérins haptiques réagissent-ils avec précision aux mouvements du télescopique ?
Nous avons travaillé en premier sur la partie « compréhension de l’environnement » en configurant les retours visuels des différents écrans ainsi que la spatialisation du son sur les enceintes. Ces périphériques servant essentiellement à de la sortie de données (affichage ou retour sonore d’une action), ils sont relativement simples à paramétrer.
Nous nous sommes ensuite attaqués aux périphériques « d’interaction » comme le volant, les joysticks, les pédales, et les différents outils du tableau de bord comme les Interfaces Homme-Machine ou IHM. Ces périphériques permettent d’interagir avec le véhicule en réalisant une action (allumer les phares, freiner, monter le télescope…). Nous avons donc relié tous les contrôleurs au simulateur et minutieusement paramétré leurs actions. Chaque élément a été testé puis ajusté afin de correspondre à la réalité.
Enfin, nous avons préparé les données télémétriques pour assurer la liaison avec le système haptique de vérins. On entend ici, les coordonnées, le poids, les états… Ces données transmises au système haptique permettent aux vérins de s’actionner pour simuler une pente, le chargement ou déchargement d’une palette ou encore une décélération.
Grâce au logiciel intégré au système haptique, nous avons ajusté et calibré chaque paramètre en récupérant des données en temps réel (position, actions…).
Après cette phase de fine-tuning, le simulateur est désormais pleinement opérationnel, prêt à offrir une expérience ultra-réaliste et interactive.
DEFINITIONS
- La Technologie Haptique : Quand le Virtuel Devient Tangible
L’haptique, issue du mot grec haptesthai (« toucher »), désigne l’ensemble des technologies qui stimulent le sens du toucher et du mouvement. Son objectif ? Reproduire la sensation d’interagir avec des objets physiques, même dans un environnement entièrement numérique.
Comment fonctionne l’haptique ?
Tout comme le graphisme et l’audio ciblent la vue et l’ouïe, l’haptique s’adresse directement au système somatosensoriel (le toucher et la proprioception). Grâce à des forces, vibrations et mouvements, elle enrichit l’expérience utilisateur en ajoutant un retour physique réaliste.
Des exemples du quotidien Nous utilisons déjà l’haptique sans forcément nous en rendre compte : - Smartphones et tablettes : la légère vibration d’un téléphone lorsqu’on tape sur son clavier.
- Automobile : le retour de force d’un volant lorsqu’on quitte involontairement sa voie.
- Jeux vidéo : le grondement d’une manette qui réagit aux explosions ou aux chocs dans un jeu.
L’avenir de l’haptique :
Bien au-delà de ces applications, la technologie haptique évolue rapidement et s’impose dans des domaines variés : simulateurs de formation, réalité virtuelle, interfaces industrielles, santé, robotique… Elle repousse les frontières de l’interaction homme-machine et façonne déjà les expériences immersives de demain.